Flexible Metal Hoses
At Quality Flex, we deliver high quality high pressure flexible metal hose to OEM engineering companies for various industrial applications. They are designed with annular or helical profiles and are available in standard or close-pitch configurations. Our flexible metal hoses are engineered for durability and are resistant to extreme temperatures (-200°C to +650°C), corrosion, and mechanical stresses such as vibrations from pumps or compressors.
Their convoluted cores, made from stainless grades such as 304, 321, and 316L that conform to international quality standards with single or multiple layers of wire braiding for high-pressure environments. Each hose assembly consists of a corrugated, leakproof, and pressure-bearing core, reinforced with wire braiding to absorb longitudinal forces and provide radial support. Our flexible metal hoses can be equipped with PTFE liners for improved chemical stability or protective outer wire coils for mechanical durability. They are available in sizes ranging from 6mm (1/4″) to 250mm (10″). We also offer customized options, including highly flexible close-pitch hoses for special applications.
Fill in the form details below. Our support team will get in touch with you.
Construction of Flexible Metal Hoses
A flexible metal hose is composed of four essential components:
Corrugated Tubing
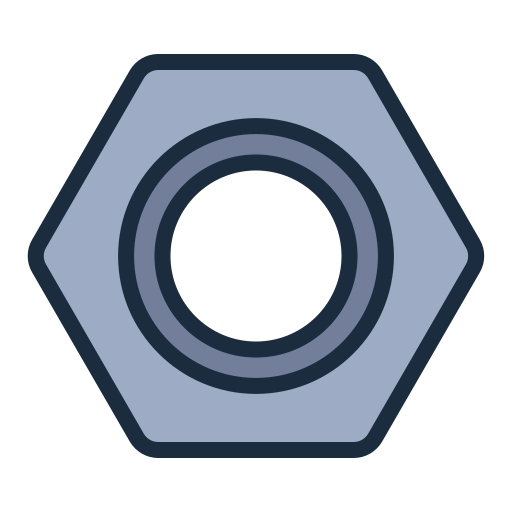
Corrugated Tubing serves as the primary element of the metal hose that provides flexibility, corrosion resistance, and pressure handling capability. The tubing’s flexibility can be increased with close-pitched corrugations to distribute bending stress effectively. The hose’s capacity to handle internal pressures is indicated by the pressure rating.
Braid
Braid is a critical component that allows the hose to withstand high pressures. The braid’s effectiveness depends on factors such as wire diameter, braid coverage, and the number of carriers in the braiding machine. A tightly woven braid with high coverage improves the pressure rating and prevents deformation. This, as a result, extends the life of the assembly.
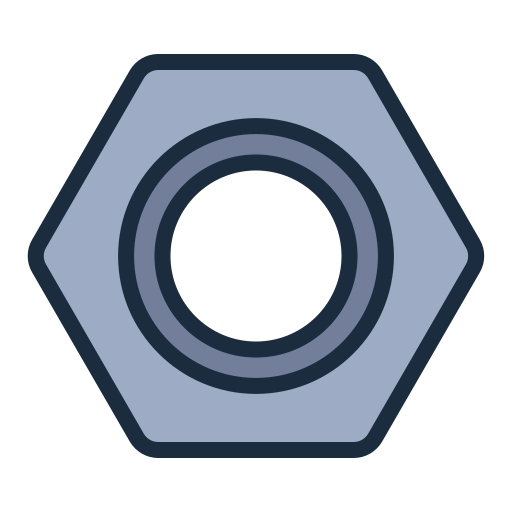
Braid Collars
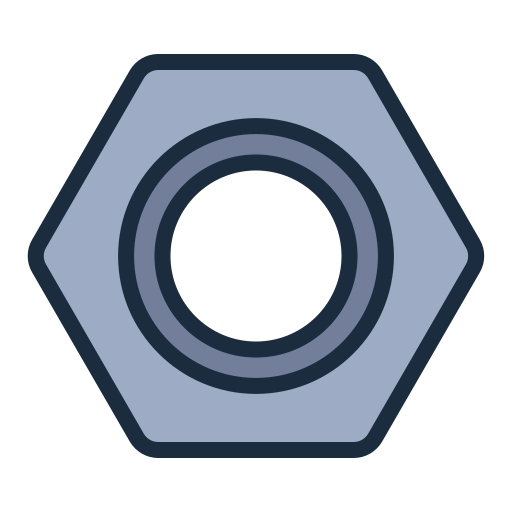
Braid Collars play a vital role in securely joining the corrugated tubing and braid into a cohesive unit. During the cap welding process, these collars protect the corrugations near the weld. This prevents damage and maintains the integrity of the assembly. They also help evenly distribute bending stresses across the corrugations. As a result, the durability and service life is extended.
End Fittings
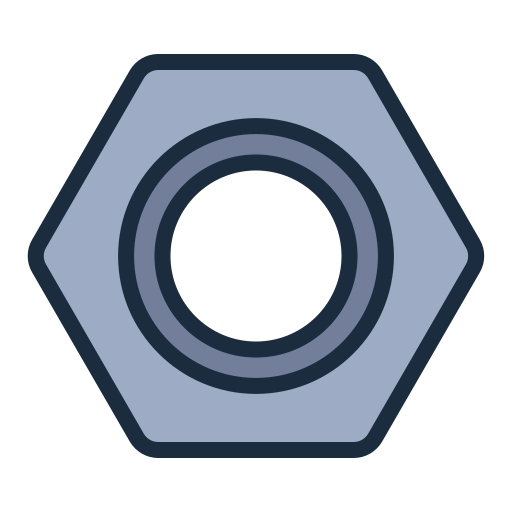
End Fittings are the final components that provide a connection interface between the hose and the application. Available in various sizes, alloys, and configurations, end fittings allow for customization to meet specific operational requirements. Proper selection of fittings is crucial as it provides compatibility with the application’s size, pressure, and material needs.
Types of Flexible Metal Hoses
Quality Flex Flexible metal hoses can be designed in two types: corrugated stainless steel hoses and interlock hoses.
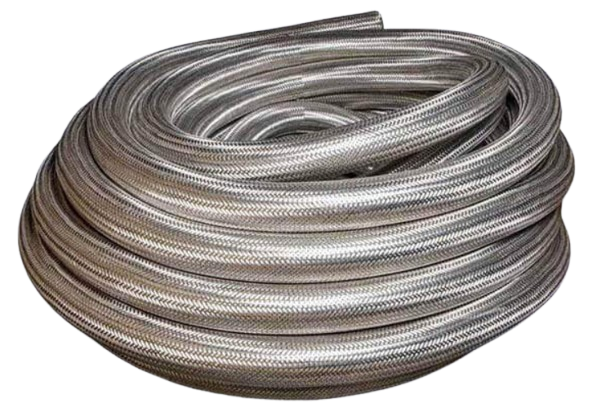
Corrugated Stainless steel hoses are built to handle internal pressure while maintaining flexibility. They are made up of a corrugated metal tube that can expand and contract without squirming under longitudinal pressure stress. These hoses are often wrapped with braided stainless steel coverings that provide additional support and protect the corrugations from wear. This improves durability and prevents damages.
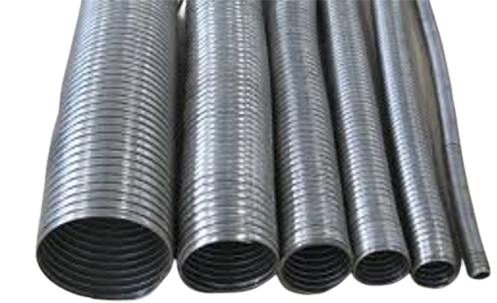
Interlock hoses are designed with a unique construction that involves interlinked rings or strips that allow for limited axial movement, and in turn, it enables the hose to flex during installation. As the hose bends, the clearances between the links gradually close, and when fully closed, the hose stiffens to signal its bending limit. Interlock hoses have a smooth outer surface, making them easy to handle without additional protective covering.
Quality Management for Flexible Metal Hoses
At QualityFlex, every production stage of our flexible metal hoses is closely monitored by qualified QC engineers. Our facility features a fully-equipped in-house laboratory and testing capabilities, adhering to international standards for metallic flexible hoses. Each flexible metal hose pipe undergoes hydraulic testing at 1.5 times the working pressure before dispatch, with additional pneumatic testing as necessary.
We rigorously inspect all raw materials used in our metallic flexible hoses, including hoses, braiding, and end connections, to ensure the highest quality standards. Our quality management process includes:
- Flex Fatigue or Cycle Life Test
- Burst Pressure or Yield Test
- Bend Radius Test
- Flame Test
This thorough approach ensures that our flexible metal hoses deliver exceptional performance and reliability.